SLFSBV01 Floating Ball Valve 150 to 600 Class
February 7th, 2018 by Amanda Schumann
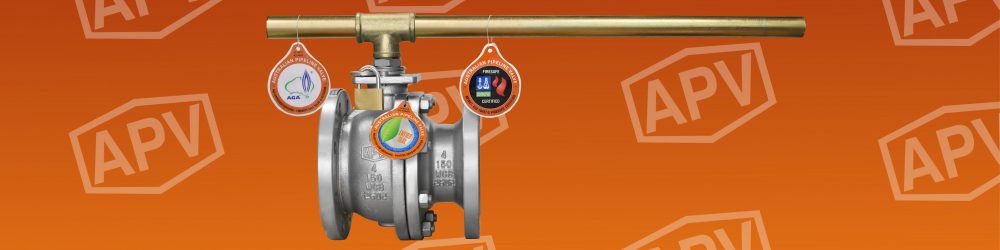
Australian Pipeline Valve’s floating firesafe SLFSBV01 ball valve design has been further improved over the last 10 years.
Features: –
- Heavy wall to API608 and ANSI B16 with high tensile heavy bolts (not Taiwan/ China style with hardware store bolts).
- Heavy T-Bar pole lever (100NB and above).
- Superior TFM1600 PTFE seats. (TFM1600 is a modified version of PTFE that maintains the exceptional chemical and heat resistance properties of PTFE but has a significantly lower melt viscosity). The result is reduced cold flow, porosity, permeability and void content. Surfaces are smother and reduce torques. The APV seat design is energised ‘heal & toe’ design with a large contact face. We stock spare seats in PEEK, Graphite and carbon filled PTFE.
- Our direct mount pad version is now designed to allow adjustment of gland packing without disassembly of other upper components (as is a requirement of oil and gas companies). Also our design has a longer packing chamber which removes the requirement for a FKM or Viton stem seal which can be compromised by temperature or chemicals in media. All parts are full stainless steel. This version also utilises Belleville spring washers for constant live loading of packing
- In all models the seat design is now improved as shown below.
- Round body design or straight edge (not China style scalloped) octagonal/hex body in smaller sizes.
- DNV witness firesafe and fugitive emission certified in carbon and austenitic in all sizes & classes.
- AGA approved.
- APV ball valves are all tested with high pressure hydrostatic and low pressure pneumatic seat tests. (Note: with this API598 is optional but APV do it as standard).
Click here to view examples of APV drawings
Seat Design
Standard floating ball valves with friction fit seats seal well either under high pressure or low pressure conditions depending on their tightness. However, being too tight causes torque problems, which combined with impurities in the line can cause jamming. If not tight enough the valves can leak at very low pressure especially with air, gas or diesel. The problem is compounded by poor quality out of round balls and stem machining. This necessitates the seat to be even tighter to affect a seal.
Also poor inflexible seat designs made in China have to be bolted up too tight to get them to pass test! Also inconsistent Chinese spiral wound body gasket thicknesses further hinders a consistent closure pressure (APV valves use an encapsulated double body gasket or a spiral wound gasket). APV balls and seats are manufactured to high tolerances.
If a valve is in service that experiences both high and low pressure during the life of its service there will be a compromise between its effectiveness and the life span of the seat. Its all very well to tighten up the traditional friction fit PTFE seats up tight but Teflon has some ‘memory’ and long term stress will eventually cause the seat to deform. The solution is to utilise the APV semi-flexible lip and heel seat design which are semi-flexible but still rigid enough to ensure seats accommodate high pressures without deformation whilst the light touch large seating face provides a bubble tight seal at low pressure. The larger seating face of the APV design is also less prone to leakage from small scratches than competitor’s small surface area light touch flexible seat designs.