AUTOMATIC CHECK VALVES
March 30th, 2016 by Sue Ey
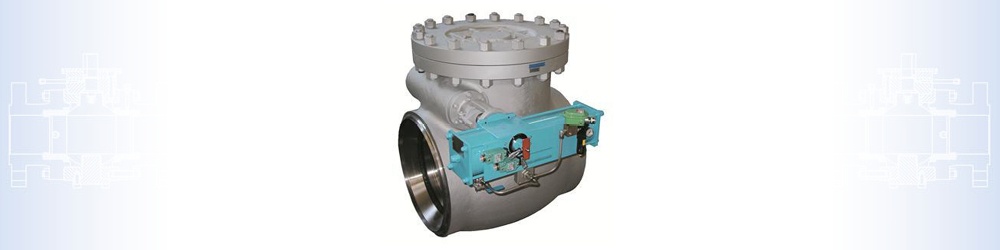
- Dampening & speed controlling with counter weights & dampeners & counter balance spring, etc.
- Testable
- Swing & tilt types
- Metal or soft seat
- API6D full port piggable
Usually the actuator is composed of a pneumatic cylinder with a single effect piston, counterbalanced by a spring. The actuator is mounted on one side of the swing check valve body and connected to the valve disc by means of a shaft. The actuator air pressure range is typically between 4 and 11 bar. Under manual operation conditions, compressed air is fed in the cylinder to load the spring and the check valve is free to operate automatically in conventional way. In the upset or emergency condition of the turbine the compressed air is vented, the spring is free to extend inside the cylinder and the actuator piston rotates the valve disc to intercept the steam bleeding pipe. The main function of the spring is to overrun the starting friction on the packing and pivot bearings. Besides the usual optionals, we can supply also valves with: – anti-rotating, anti-oscillating feature; – damping device on the shaft operating the valve disc; – three-way valve (to be installed on the compressed air feed line) manually operated by a spring loaded lever (the spring is needed to run back the lever in the valve closed position) to test during maintenance the operation of the check valve and actuator; – micro switches on the actuator for the indication of: – check valve open during normal operation, – check valve closed.
SIZE RANGE
4″ to 42″ (DN 100 to 850) for ASME Class 150-300 4″ to 20″ or 16” (DN 100 to 500) for ASME Class 600 4″ to 12″ (DN 100 to 300) for ASME Class 1500 4″ to 8″ (DN 100 to 200) for ASME Class 2500.
RATING
ASME Class 150, 300 Bolted Bonnet ASME Class 600 Pressure Seal Bonnet and Bolted Bonnet ASME Class 1500 Pressure Seal Bonnet ASME Class 2500 (PN 420) Pressure Seal Bonnet.
MATERIALS
Carbon Steel, Alloy Steel, Stainless Steel and others on request.
Click here for more information on Automated valves.
Swing disc and Testable Pneumatic check valves are manufactured with Bolted Bonnet or Pressure Seal Bonnet design. Tilting disc check valves are manufactured Pressure Seal Bonnet design. Check valves are straight-through valves usually operated automatically. The Testable Pneumatic check type is equipped with a safety pneumatic adapter that provides assistance to the valve at the beginning of closing operation.
SWING DISC TYPE – TESTABLE VALVES
This design lends itself to numerous on-off and ESD applications. These special types of swing-disc or tilt disc check valves are usually installed on the turbine steam bleeding lines of the feed water preheating stages of modern power station cycles. The main function is the quick shut off of the bleeding steam pipes in case of loss of turbine load to prevent the dangerous water carryover from the preheater back to the turbine. In the upset or emergency condition of the turbine, the compressed air is vented, the spring is free to extend inside the cylinder and the actuator piston rotates the valve disc to intercept the steam bleeding pipe. The main function of the spring is to overrun the starting friction on the packing and pivot bearings.
We can also supply valves with:
– anti-rotating, anti-oscillating feature;
– damping device on the shaft operating the valve disc;
– three-way valve (to be installed on the compressed air feed line)
manually operated by a spring loaded lever (the spring is needed to run back
the lever in the valve closed position) to test during maintenance the operation
of the check valve and actuation;
– Microswitches on the actuator for the indication of:
– check valve open during normal operation,
– check valve closed.
POWER STATION TURBINE STEAM BLEED LINES ON FEED WATER PREHEATING
Excessive overspeed of a turbine-generator shaft can be disastrous, the energy contained in the feedwater heaters of a steam power cycle is often sufficient to take turbine to overspeed. This energy in the stream is contained in the turbine extraction piping (“bleeding” lines), in the water is contained in the heater shell and in the metal parts.
After a load rejection, the steam admission valves will close causing the pressure of steam, already in the turbine, to decay.
This decay allows the steam in the extraction piping and heater shell to flow back into turbine giving its energy back to turbine rotor.
Therefore, immediately after an electrical load rejection or turbine trip, this stream flow inversion must be prevented by some mean. The mot common of which is by the use of Pneumatic Operated Testable Check Valves.
The pneumatic actuators that control the swing check valves, installed on the turbine’s bleeding lines, are single effect type: air to open/spring to close.
During the normal operation the actuator spring is compressed by the air feeding the actuator piston.
In the need of a fast and effective check valve closure, the air is dumped from the lower chamber of the piston and the spring does extend.
Through a system of a fork-lever-control shaft or with a rotative actuator a torque is transmitted to the swing arm, sufficient to close the valve disc against its seat.
The linear or rotating movement impressed to the piston by the actuator spring is transformed into a rotating movement by the “claw-clutch” operation of the lever onto the valve lever control shaft.
When the actuator spring is free to extend, for closing the valve, the lever control shaft does not immediately engage on to the swing arm but for a 5″ angular rotation, being free to move, accumulates kinetic energy so that the rotation is transferred to the swing arm in an impulsive way like a hammer blow.
Such an impulse make sure to overcome any static friction not only due to the contacts between the various valve components but also any other friction derived from the oxidation of parts.
Due to such unknowns the force that the spring must exert, the valve is sized to overcome the known friction forces by a factor of 4.
To reduce the friction forces we usually install, as packing, pure commercial graphite rings.
When it is specifically necessary to reduce the pressure drop, the angular opening of the swing disc is increased.
For such reason a counterweight is installed on the arm pin on the side opposite to the actuator. In this case the check valve swing arm is no longer free to rotate respect to the arm pin but instead is keyed on to it.
In the latter case the arm pin, protruding outside the valve body, needs to be sealed.
Pure commercial graphite rings are used in the stuffing box.
For such application it is advantageous if the disc seat is positioned at 90º respect to the steam flow and the body, afterwards the seat, is bulged to allow a sufficient pressure recovery which ensures a low overall pressure drop.
Swing check valve with 90º seat
Swing check valve with inclined seat
Emergency Fire Shut Off Valves Fuseable Link – Self Closing